SUCCESS STORIES
Our ability to problem solve and create practical manufacturing solutions is what allows us to work with the top food manufacturers globally.

GMS Cup Drop Assembly
The Problem
A customer was experiencing frequent jams in their cup drop system, which caused unplanned machine stoppages. These interruptions led to significant product spoilage and bottlenecks in production — severely impacting throughput and reliability.
Our Solution
We completely redesigned the cup drop assembly, incorporating higher-grade materials, optimized cup spirals, and a vacuum-assisted seating mechanism. This allowed cups to be reliably placed into trays without sticking or misalignment.
The Results
- Eliminated unscheduled downtime due to cup jams
- Improved product handling and tray alignment
- Nearly doubled throughput by maintaining consistent operation
With a more reliable, efficient system, the customer now runs their line with significantly fewer interruptions and increased confidence.
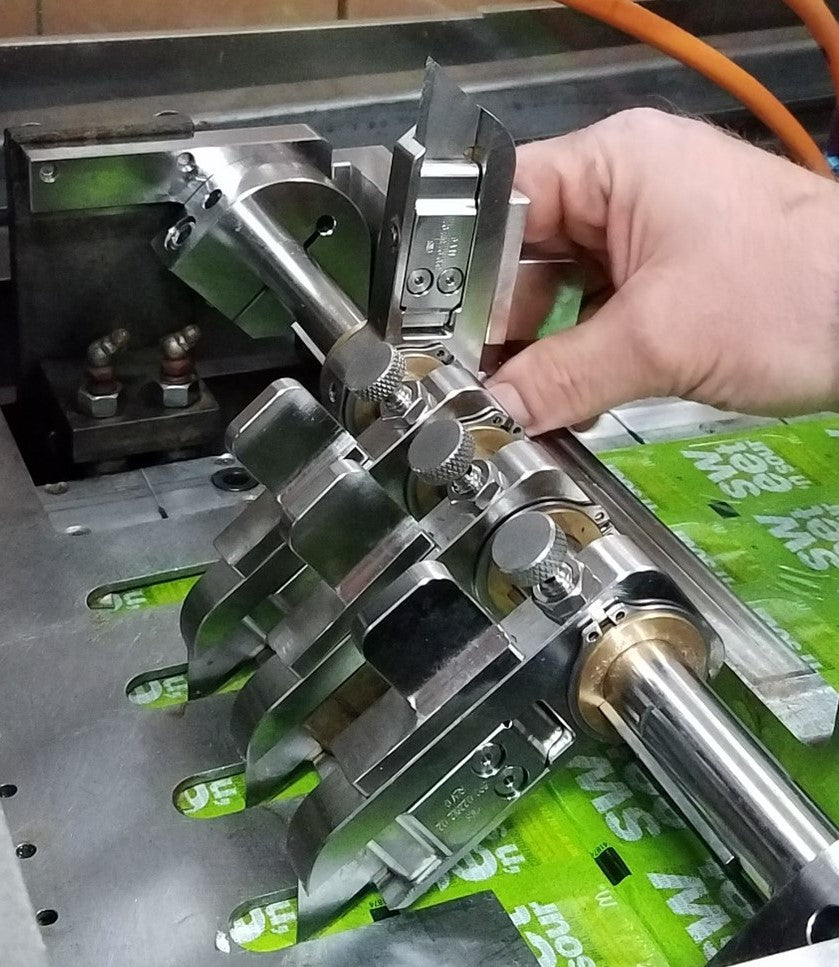
GMS Quick Change Slitter Assembly
The Problem
A customer approached us following a serious injury sustained during blade replacement on their existing slitter knife assembly. The OEM unit required removing bolts and rotating up an assembly that exposed four sharp blades at once. To change a blade, operators had to reach across the exposed knives with a wrench — a risky process that led to a major injury and downtime.
Our Solution
We designed and built a quick-change, toolless slitter assembly that prioritizes safety and efficiency. Each knife holder rotates independently into a locked maintenance position, exposing only one blade at a time. A top-mounted lever allows the blade to be accessed and replaced without tools or reaching over sharp edges.
The Results
- Eliminated simultaneous exposure to multiple blades
- No tools required for blade replacement
- Safer, more ergonomic maintenance procedure
- Reduced blade change time from 20 minutes to under 5 minutes — a 75% time savings
This redesign not only eliminated the safety hazard but also significantly increased operational uptime.
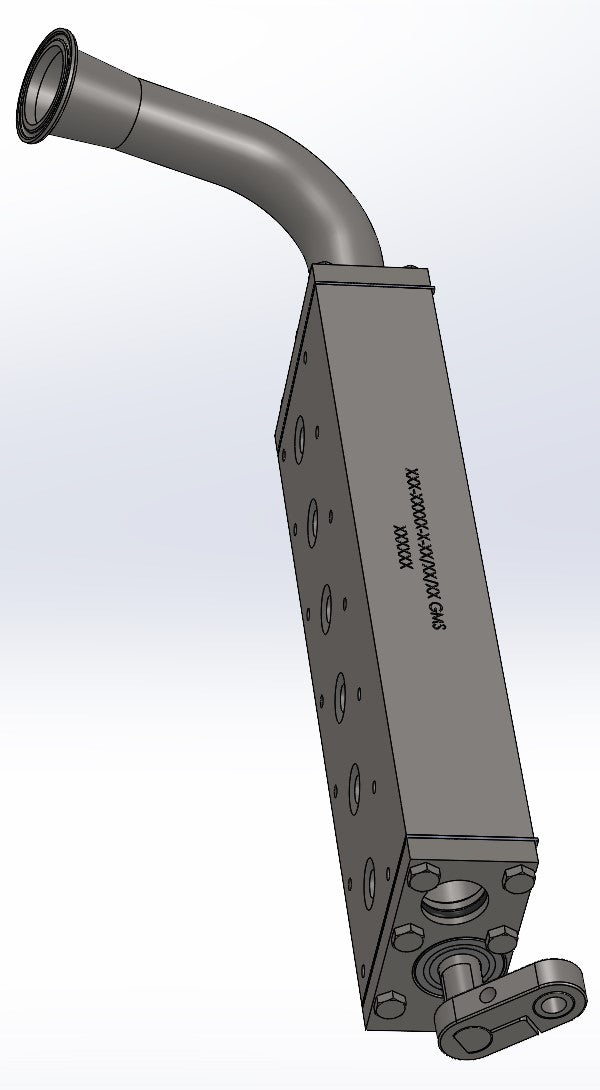
GMS Precision Rotor Fillers
The Problem
A major food processing company using vertical form fill equipment was experiencing frequent rotor filler failures. Their existing OEM parts required rebuilding every 4–6 months, contributed to leaking pouches, and delivered inconsistent fill weights — all leading to product loss and frequent downtime.
Our Solution
GMS developed and introduced the GMS Precision Rotors, engineered to outperform traditional metal-to-metal OEM designs in durability, accuracy, and sealing performance.
The Results
- Exceptional Longevity: Predicted to last 18 months (3× OEM lifespan), several units are still running reliably after 36 months — a 600% increase.
- Lower Maintenance Costs: Reduced rebuild frequency and eliminated related machine downtime and labor.
- No More Leaks: Complete elimination of leakage issues associated with the rotor filler.
- Improved Fill Accuracy: More consistent pouch-to-pouch fill weights, reducing overfill waste and improving efficiency.
The GMS Precision Rotor has become a long-life, high-precision replacement solution trusted in demanding production environments.